"Overall the experience was excellent for all involved and we would gladly use your services again; please pass on our comments and gratitude."
> see more
Positive Activities for Young People Team Leader, Luton Borough Council
Health and Safety consultants and consultancy, UK
Noise Risk Assessments
What do the New Noise Regulations require you to do?
The Control of Noise at Work Regulations 2005 came into force for all industry sectors in Great Britain on 6th April 2006 (except for the music and entertainment sectors where they came into force on 6th April 2008). The aim of the Regulations is to ensure that workers' hearing is protected from excessive noise at their place of work. Exposure to high noise levels can cause hearing loss and conditions such as tinnitus (permanent ringing in the ears).
These new regulations place more stringent requirements upon the amount of noise to which workers can be exposed. Employers must provide hearing protection and hearing protection zones when workers exceed the Upper Exposure Action Value (which is a daily or weekly exposure of 85dBA or more). Above the Lower Exposure Action Value (which is a daily or weekly exposure of 80dBA or more), employers must assess the risk to workers' health and provide them with information and training. There is also an Exposure Limit Value of 87dBA, taking account of any reduction in exposure provided by hearing protection, above which workers must not be exposed.
Noise risk assessments are essential to understand whether working conditions conform to these new regulations.
Noise Risk assessment: The Next Step...
If you feel that you may need a noise risk assessment within your workplace, your first step should be to contact us for an informal chat. This will help us to understand the issues within your workplace and enable us to suggest an assessment programme to satisfy both the current legislation, as well as your own needs. Any noise at work risk assessment involves a consultant spending some time at your site, taking noise measurements, and then writing the report.
Why use an RSA Consultant for Noise Risk Assessment?
The new Control of Noise at Work Regulations 2005 call for the use of ‘expert intermediaries’ meaning an employer should rely on competent third parties where they themselves are not competent for the relevant aspect of noise in the workplace.
Noise risk assessment can be very complex and you need the right combination of training and experience to be considered as competent. RSA ’s consultants are members of both the Institution of Occupational Safety and Health as well as the Institute of Acoustics, which is the gold-standard of competency in noise assessment.
Consultants such as those at RSA use only modern, data logging sound level meters. Old sound level meters or very simple units give only an instantaneous level of noise in decibels, which makes it difficult to look at the value on the display and assess an average value. This problem is compounded by the fact that machine noise that sounds ‘steady’ to the ear can vary by 3dB. A 3dB increase is a 100 per cent increase in noise energy, meaning that large errors can be made if an accurate average is not measured.
This is why modern sound level meters have an averaging feature called Leq. This is called the equivalent continuous sound energy level. As this value uses the ‘A’ weighting, this is normally displayed as LAeq when written down.
About Noise Risk Assessments
Noise Risk Assessments: Measuring Sound Level
The regulations are designed to protect individuals from damage to their hearing, both from exposure to sustained levels of noise over a working life, and from very high impulses of noise, which can give instant damage. With this in mind, measurements are taken which assess the average exposure an individual is subjected to throughout the day and also measure any ‘peaks’ of noise which could result in instant hearing damage.
Noise Risk assessment: How do we Calculate Noise?
In order to compare different industries and shift times in a way that the same action levels can be used, noise exposure is standardised to an eight hour working day value called LAEP,d (‘daily personal noise exposure). When measuring the LAeq it is important to measure for a period of time that is representative of the employees’ exposure and what the exposure time is for that noise. If an employee performs different jobs (and hence experiences differing noise levels) it will be necessary to repeat this for each different job, noting the exposure time for each.
If people are likely to be exposed to high levels of impulsive noise, such as noise emitted from heavy pressing operations or sheet metal working, then the peak noise must be measured.
Noise Risk assessment: Two Approaches to Noise Assessment
The two main methods for the measurement of noise are either to use a sound level meter or a noise dosimeter. A sound level meter is primarily designed as a hand held meter, whereas the noise dosimeter is worn by an employee for his or her working shift. A common misconception is that if you have to measure noise dose, you use a dosimeter. In fact the HSE’s preferred method of measurement for noise surveys is to use a sound level meter.
There are several reasons for this, primarily because when performing a noise survey with a sound level meter the operator is present and measuring the noise of the employee. This ensures there are good quality measurements that are repeatable. With a sound level meter, a representative measurement is made for each job function and the exposure time for each, and from there the eight hour exposure can be calculated.
The more complex the work pattern of an employee becomes, the more the difficulty to assess the noise dose using a sound level meter is increased because more and more measurements would need to be taken in order to calculate noise dose.
A noise dosimeter consists of a microphone on a cable, which can be clipped to the lapel or collar. The dosimeter can then be started at the beginning of the shift. Another useful feature of noise dosimeters is that they will ‘log’ the noise data so that, when downloaded to a PC, the time history of the noise can be viewed. This gives the ability to analyse when and where high noise exposures occur through a shift. This can be even more useful when the dosimeter can be placed on an employee who is prepared to make a diary of what times and jobs he or she was performing throughout the day. This will give the employer the ability to directly see which operations most need noise control in order to reduce noise exposure.
Noise Risk assessment: Checking for the Right Level of Protection
Although it is always the last resort, where the selection of hearing protection is required it may be necessary to measure the frequencies of the noise that are present (octave bands) to ensure that the hearing protection is giving the correct attenuation:
For advice and information on Health and Safety Consultancy and how we can help you, call 01933 626444 or email us today.
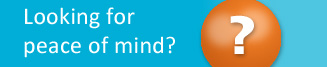
Join our Advisor Service for quick, cost-effective, 'special client' status